For this task, we were instructed to make a high poly crate that would be ready to be baked onto the low poly version.
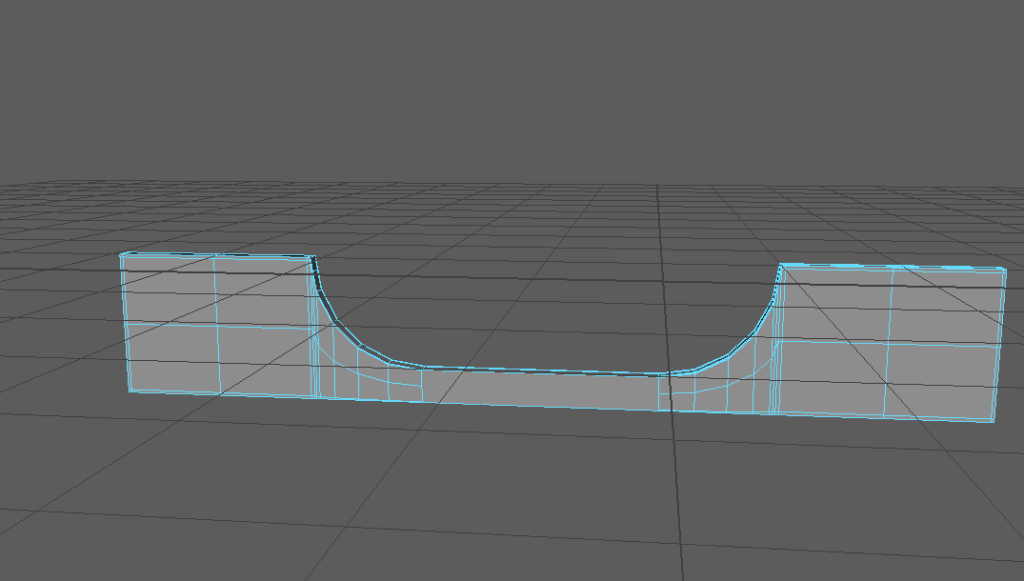
I began the task by placing a cylinder. From there, I used one face of the cylinder to eventually create the handle of the crate. The edge loops were a slight pain in this stage as some of them would not go through the entire shape, only one half. After further inspection some of the topology was distorted which was most likely causing this issue. As a result, I opted to start again, with everything going smoothly the second time around.
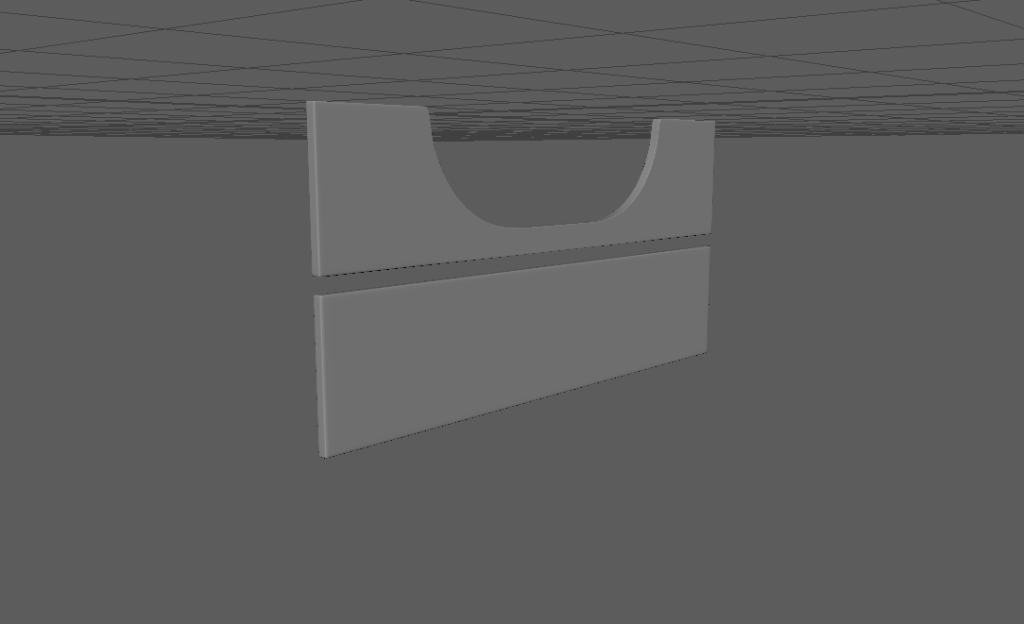
The next step was creating the separate planks for the crate. Once I had made one plank, I could just duplicate it. This was a relatively easy process.
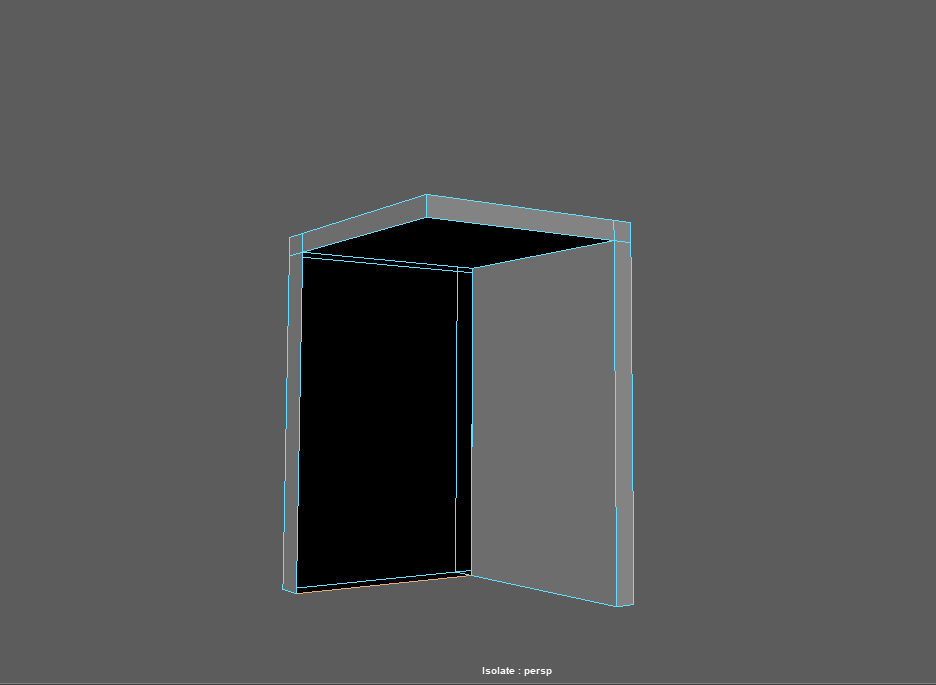
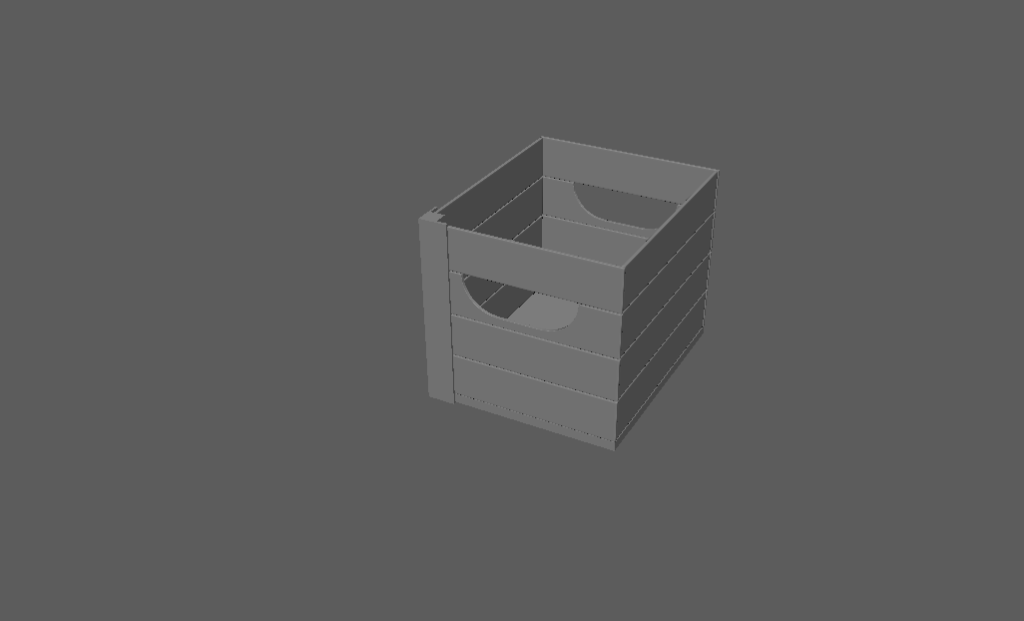
The corner piece was next. I achieved this via extruding the edge loops I had created.
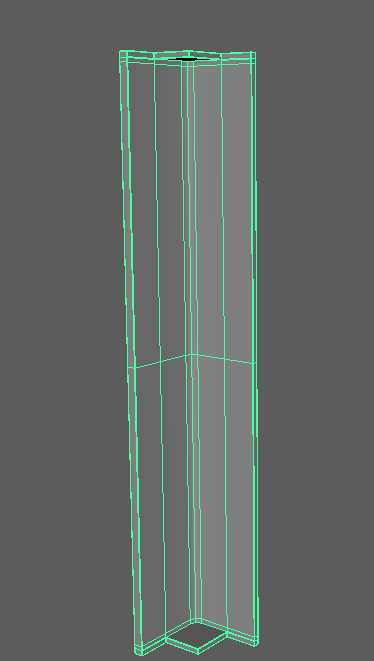
To avoid any stretching on the corner piece, I added multiple edge loops. To be as efficient as possible, I only did this for one half of the corner piece, then I mirrored it. This made the process much quicker and it also made the topology much neater as everything was identical on both halves.
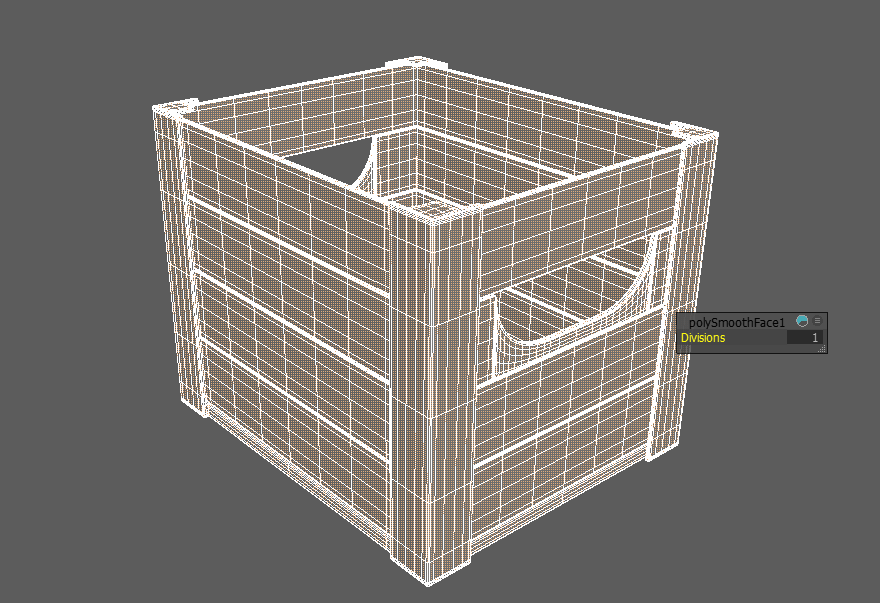
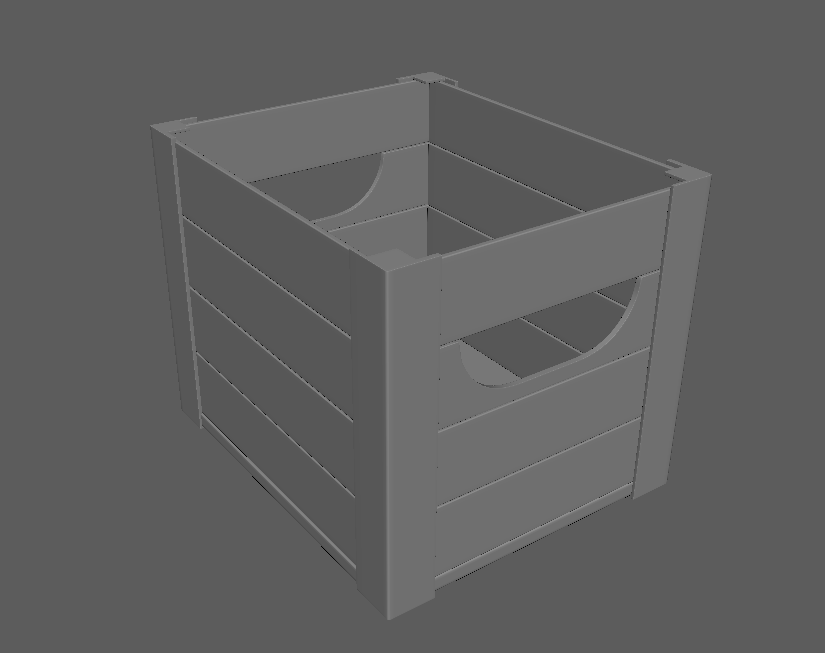
The final step for the high poly model was to smooth it. This is achieved by adding subdivisions – the more you have, the smoother the end product.
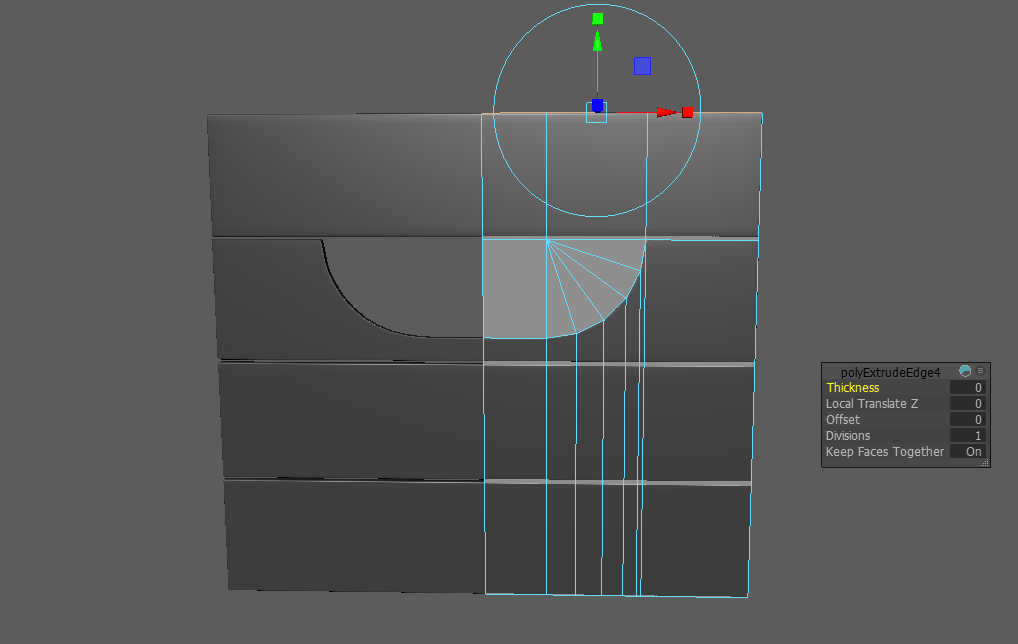
The process for creating the low poly model was repeating the same steps as before, but with less polygons. The real challenge came in making sure everything was the exact same size as the high poly model.
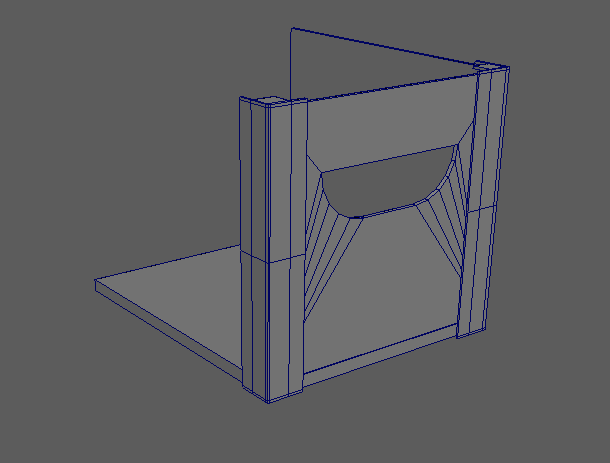
I only created two sides as both can be duplicated once the UV and substance painter processes have been completed, again making this much more efficient.
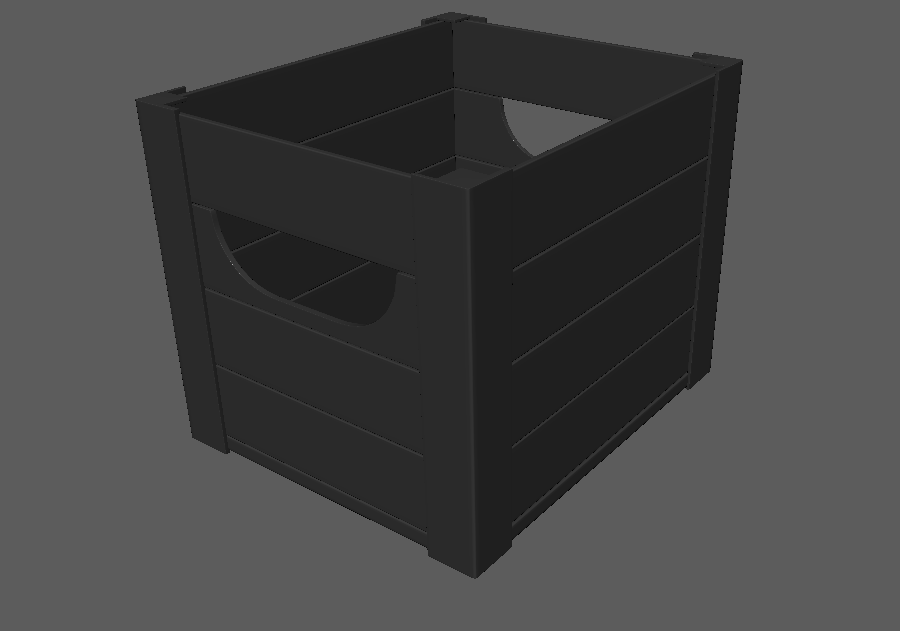
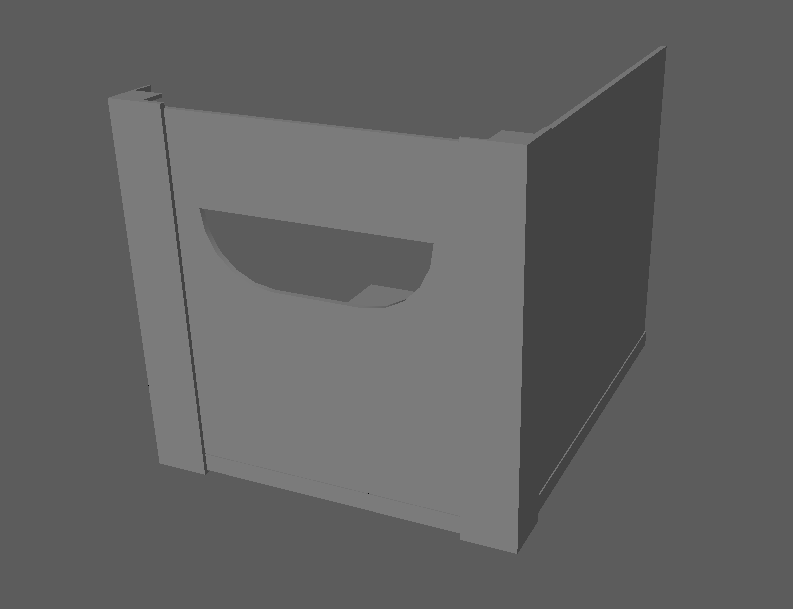
Overall, this task was helpful in making me understand the differences between high and low poly models and the importance of both of them in the process of 3D modelling.